Our Process
The Progressive Systems Difference: 5 Step Process
Responsiveness to the needs and wants of our customers, taking their lead in machine
customization, separates Progressive Systems from the rest. Listening well shapes our process
as we design and build machines for advanced manufacturing.
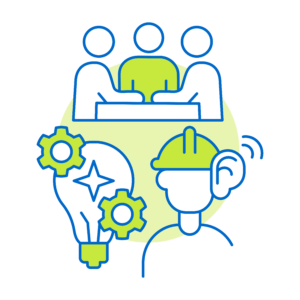
Engineering & Design
Our experienced engineers listen well and concentrate intensely on learning all the details of what you seek to accomplish. From concept to design, we invest in gaining a deep understanding of your requirements and needs.
- In-house engineering design and concepting is based on your criteria and an on-site needs assessment.
- Design meetings with your plant and engineering associates identify specific requirements for your new equipment including type of parts to be manufactured, production rates, quality requirements, and other details.
- One or more concept drawings prepared for a second review scheduled at your location, our location, or online.
- Final written proposal and engineering drawing are provided, usually including a 3D model.
Customization
Demands for specific machine capabilities and other requirements make each machine build unique. Working from decades of experience and a wide range of successful designs, every machine is fully customized to handle your precise production needs.
- Customization is based on the type of product being produced.
- Machines may be designed to offer new capabilities while fitting into an existing space.
- New designs may accommodate complex and product-specific elements.
- Drawings and layouts based on previous designs are prepared reflecting your unique customization requirements from complex specialty capabilities to high volume production rates.
Manufacturing & Testing
Progressive manufactures and builds every machine in the USA. Parts fabrication, a critical aspect of the machine building process, takes place almost exclusively in our primary Minnesota facility.
- Review progress on your machines during the fabrication and assembly stages; extensive Factory Acceptance Testing before shipment is common.
- Design reviews are planned for in the timeline for highly customized machines.
- Other milestones include fabrication complete, start of assembly, SAT (Site Acceptance Testing), shipment, receipt at customer site, and completion of FAT (Factory Acceptance Testing).
- The overwhelming majority of fabricated machine parts are fully produced in on Progressive Systems facility.
On-site Implementation
Efficient installation at your location means less disruption to existing processes. Because we dispatch large teams, on-site installations can be completed more rapidly.
- Reassembly and installation at your site is conducted by the same team involved in the design and building process.
- We send a team, not a single service tech, to handle installation and training.
- Installation is fast, supported by the techs who built the machine and the controls engineer and lead mechanical tech.
- Our team stays on site until the machine is in production.
Training, Support & Maintenance
Needs for training, support and maintenance vary greatly with type of machine and customer situation. Training is part of the installation process; customized maintenance options and support are tailored to your needs.
- In-house training after installation is included along with a custom user manual for every machine.
- Support is available on-site or remotely from our world-class service department. You’ll talk with the technicians, engineers, and sales team who were involved in designing, building, and installing your machines.
- Support benefits can be added to your order, such as a critical spare parts list, or spare parts at a discount when ordered prior to machine shipment.
- One complimentary (no labor charge) preventive maintenance inspection six months after delivery is included and discounts are available for scheduling additional future visits.
- Because we manufacture in the USA, our response to downtime or service issues is immediate–most parts can be shipped or manufactured the same day.